With the SAP Model Company to the rollout template
In last article I reported on how we started the greenfield implementation project at odelo, how we used SAP Activate as the implementation methodology, how the project was organized and what challenges we faced in terms of infrastructure and building up the team’s knowledge. I have also already briefly discussed the technical implementation of the SAP Model Company for automotive. In this article, I would like to discuss the procedure for adapting SAP Best Practices and Model Company processes to odelo.
The aim was to develop a rollout-capable template that can later be rolled out in the locations in Germany, Slovenia, Turkey, Bulgaria, China and Mexico. The template consists of process documentation as well as an S/4HANA system in which the processes are customized and can be booked through with sample data. Test scripts were created to match this.
SAP Model Company
As described in the last article, we started with the Model Company for automotive supplier V1 based on S/4HANA 1610.
It was clear from the outset that the template system would be developed on the basis of Model Company for automotive suppliers V2 and therefore on S/4HANA 1709. However, the 1709 version was not yet available at that time and was only delivered and installed after the first workshops. In order to meet the target landscape with the template processes, we used the best practices of version 1709 as the basis for process scoping right from the start.
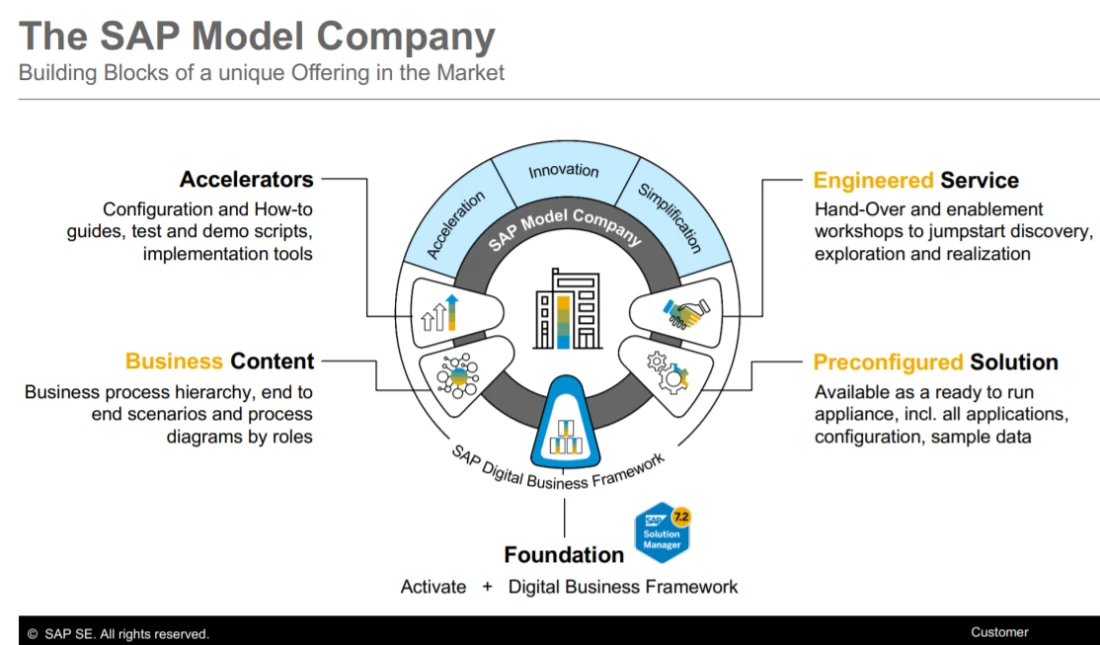
But what exactly does the Model Company involve? In terms of processes, the Model Company builds on the activated Best Practices processes of the respective release. The specific Model Company processes then make up the added value. In the case of SAP Model Company for Automotive Suppliers 1.0, these were 28 preconfigured automotive supplier-specific processes from the areas of “Order to Cash”, “Plan to product”, “Procure to Pay” and “Extended Warehousing”. Examples of these are
- O2C: Sequence call-off in sales with forwarding from distribution warehouse to production plant, EDI clearing and credit note procedure
- P2P: purchase scheduling agreement with JIT call-off
- Plan to product: Co-product manufacturing
- Extended Warehousing: Goods receipt with storage in storage bin and QM inspection
In addition to the preconfigured end-to-end processes (including master data), the Model Company provides business process diagrams for each process. Furthermore, business process descriptions are supplied in such a detailed form that it is possible to post through the processes in the system. In addition, configuration guides are supplied in which the customizing settings required for the process and, if necessary, minor programming are described in detail.
Value add services” are supplied in a bundle with the SAP Model Company. These are hand-over workshops on the part of SAP in which the specific processes of the Model Company are explained and booked through on the system. A rough fit/gap assessment is also carried out.
Template development
A major challenge in the template development was the reduction of complexity, on the one hand in the dimension of the organizations involved, on the other hand in the use of different ERP products and processes. In order to reduce the complexity, a core team was formed with key users from Germany, Slovenia and Turkey. This meant that the interests of all national companies were represented and at the same time the team had a size that enabled efficient work. We reduced the complexity of the different ERP systems through an iterative approach. First, we functionally aligned the Baan processes with the best practices and model company processes. In the second step, these processes were then compared with the SAP processes of the legacy system.
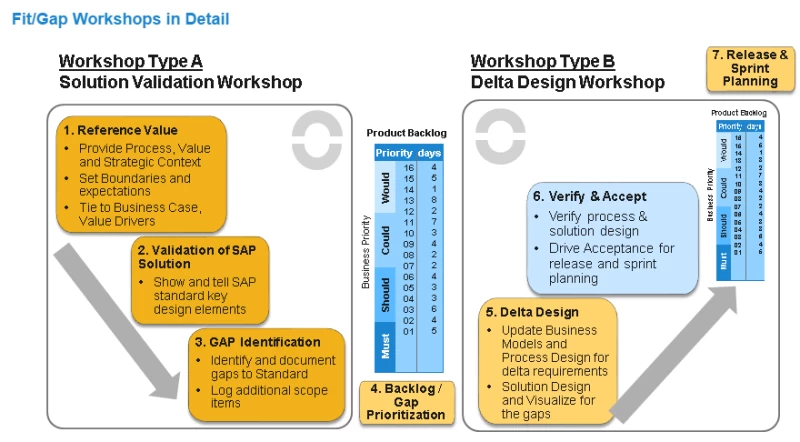
Following the joint definition of the organizational structures and the harmonized master data, the Baan processes were first compared with the Model Company and best practice processes in fit-gap workshops. In the second step, the SAP ECC processes were then compared. Once the GAPS had been identified and classified, the solutions were designed and implemented. This was done iteratively, i.e. once an area had been set up, it was tested together with the Keyuser team and adjustments were made if necessary.
The template was set up in a separate client of the development system, which was supplied with the customizing from the customizing client in the development system. At the same time, the processes were documented on the basis of the model company’s business process descriptions so that the template processes could be posted with odelo-specific data.
The testing and release of the harmonized processes marked the end of the template phase. odelo now had a customized template system with corresponding documentation and could start the rollouts.
Learn more
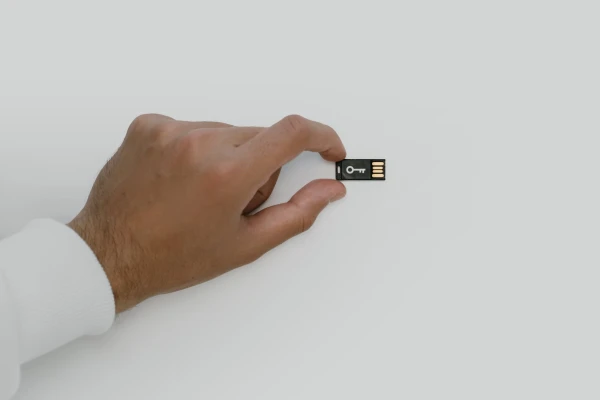
The balancing act between the requirements of the GDPR and the needs of business departments for data transparency is not easy to manage. SAP ILM can help.
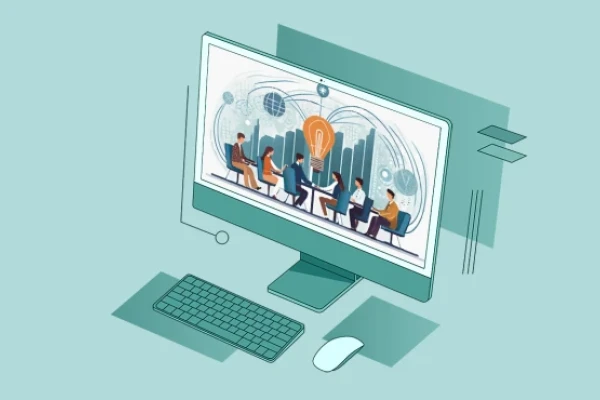
What changes and innovations can customers expect when switching to the new SAP S/4HANA 2023 release? A brief insight into the new release strategy and highlights of the new release at application level.
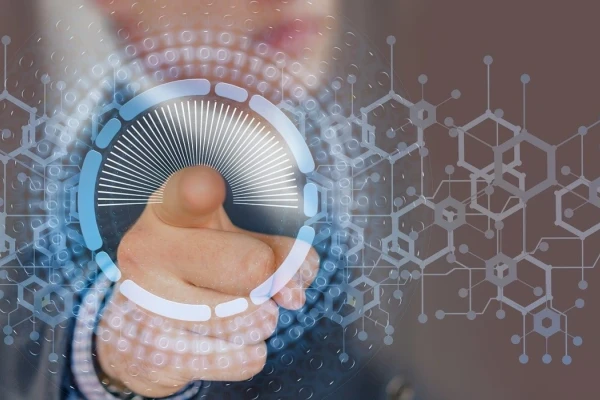
Learn how SAP S/4HANA Embedded Analytics enables you to make informed decisions with real-time analytics.
Markus Wühr
Senior Consultant
Phone: +49 173 301 2293
E-Mail: mwuehr@spirit21.com
As a senior project manager, Markus was responsible for the SAP S/4HANA implementation at odelo GmbH, among other things.
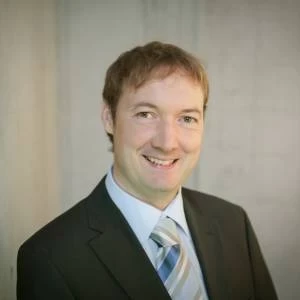